The main reasons for the occurrence of depressions and sink marks in injection-molded parts are as follows:
Large Material Shrinkage Rate
Different plastic materials have different shrinkage rates. If a material with a relatively large shrinkage rate is selected, during the cooling process after injection molding, it is likely to undergo a large volume shrinkage, thus leading to the appearance of depressions and sink marks.
For example, some crystalline plastics such as polyethylene (PE) and polypropylene (PP) have relatively large shrinkage rates. In contrast, amorphous plastics such as polystyrene (PS) and polycarbonate (PC) have smaller shrinkage rates. When selecting materials, according to the specific requirements and usage environment of the product, a material with a smaller shrinkage rate should be reasonably chosen to reduce the generation of depressions and sink marks.
Poor Fluidity
If the fluidity of the plastic material is poor, it will result in insufficient filling of the mold cavity during the injection molding process, especially in parts with a large wall thickness or complex structures, where a lack of material is likely to occur. During the cooling process, due to the lack of sufficient material replenishment in these parts, depressions and sink marks will be formed.
The fluidity of the material can be improved by adjusting the material formula, adding lubricants, or increasing the processing temperature. For example, adding an appropriate amount of flow aids to the material can reduce the viscosity of the material, improve its fluidity, and make it easier for the material to fill the mold cavity.
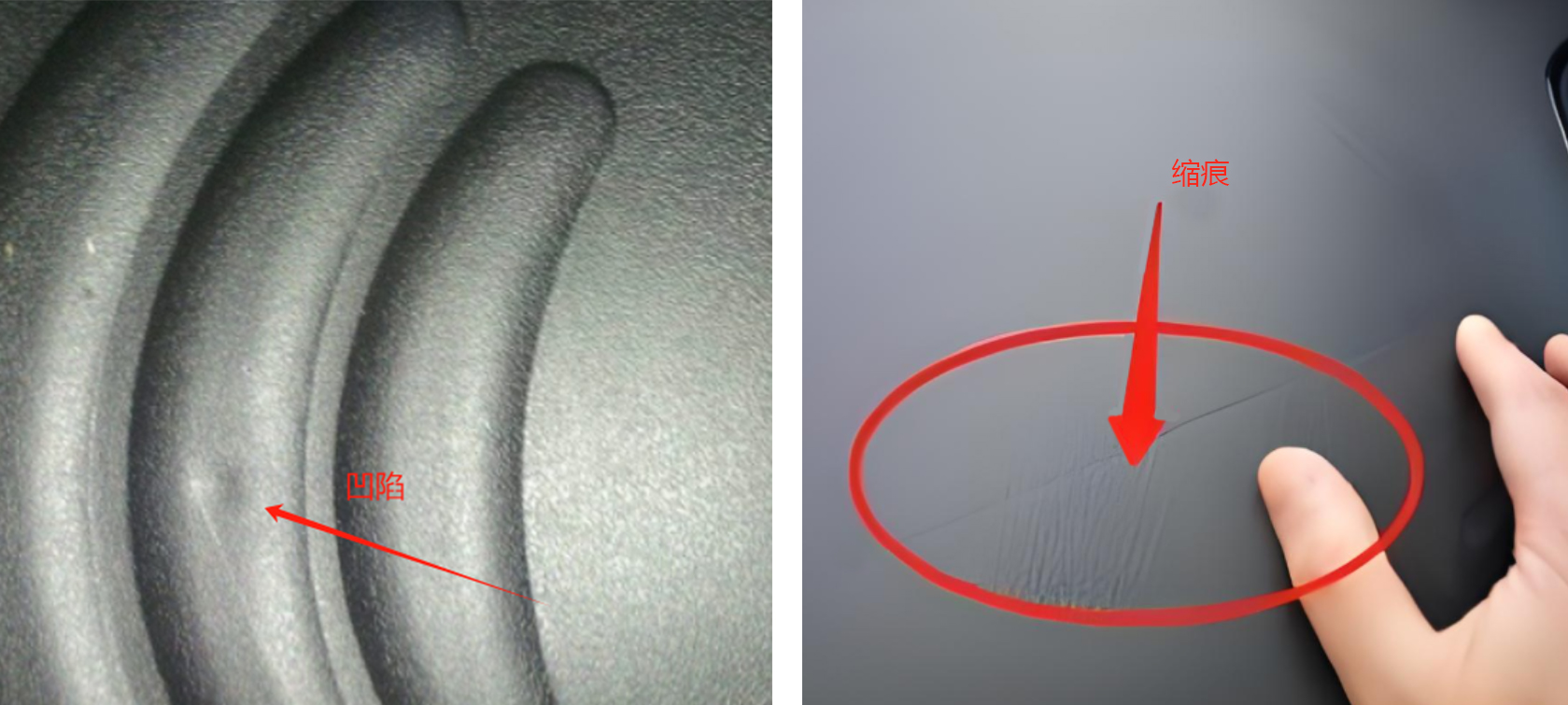
Unreasonable Gate Size
If the gate size is too small, it will limit the flow rate and flow volume of the plastic melt, resulting in insufficient filling of the mold cavity. Especially in the parts far from the gate, depressions and sink marks are likely to occur.
If the gate size is too large, excessive heat will be generated at the gate of the plastic melt, causing the material to cool and solidify prematurely, affecting the subsequent filling and pressure holding processes, and also making it prone to depressions and sink marks.
The size and position of the gate should be reasonably designed according to factors such as the size, shape, and wall thickness of the injection-molded part. Generally, the gate size should be moderate, which can not only ensure the smooth flow of the plastic melt but also avoid excessive heat generation and pressure loss.
Uneven Mold Temperature
Uneven mold temperature will cause uneven shrinkage of the injection-molded part during the cooling process, resulting in depressions and sink marks. For example, if the local temperature of the mold is too high, the plastic melt in this part will cool slowly and shrink more; while if the local temperature of the mold is too low, the plastic melt in this part will cool too quickly and shrink less.
The uniformity of the mold temperature can be improved by optimizing the cooling system of the mold. For example, setting up a reasonable cooling water channel in the mold to ensure that the flow rate and volume of the cooling water are uniform, so as to keep the temperature of each part of the mold consistent. At the same time, equipment such as heating rods or oil temperature machines can also be used to heat the mold to improve the temperature uniformity of the mold.
Unreasonable Cavity Design
Uneven wall thickness of the cavity will lead to uneven shrinkage of the injection-molded part during the cooling process, resulting in depressions and sink marks. For example, the part with a larger wall thickness shrinks more, and the part with a smaller wall thickness shrinks less, and depressions and sink marks are likely to occur at the position where the wall thickness changes.
When designing the cavity, the wall thickness should be kept as uniform as possible to avoid large changes in wall thickness. At the same time, the surface finish of the cavity should be improved, and the surface roughness should be reduced to reduce friction and improve the fluidity and filling ability of the material.
In conclusion, the generation of depressions and sink marks in injection-molded parts is the result of the combined action of multiple factors such as materials, molds, and processes. In actual production, according to the specific situation, these factors should be comprehensively analyzed, and corresponding measures should be taken to reduce the generation of depressions and sink marks and improve the quality of injection-molded parts.