Good maintenance of injection molds can extend their service life, improve production efficiency, and enhance product quality.
Inspect the Appearance of the Mold
Carefully check whether there are situations such as rust, scratches, and deformation on the surface of the mold. If problems are found, they should be dealt with in a timely manner, such as removing rust, polishing, or repairing the deformed parts.
Check whether the channels such as the cooling water holes and ejector pin holes of the mold are unobstructed. If there is any blockage, it should be cleared in a timely manner.
Clean the Mold
Use special mold cleaning agents and soft cloths to clean the oil stains, dust, and remaining release agents on the mold surface. Ensure that the mold surface is clean to avoid affecting the appearance quality of the products.
For molds with complex structures, compressed air can be used to blow away the dust and debris in the gaps.
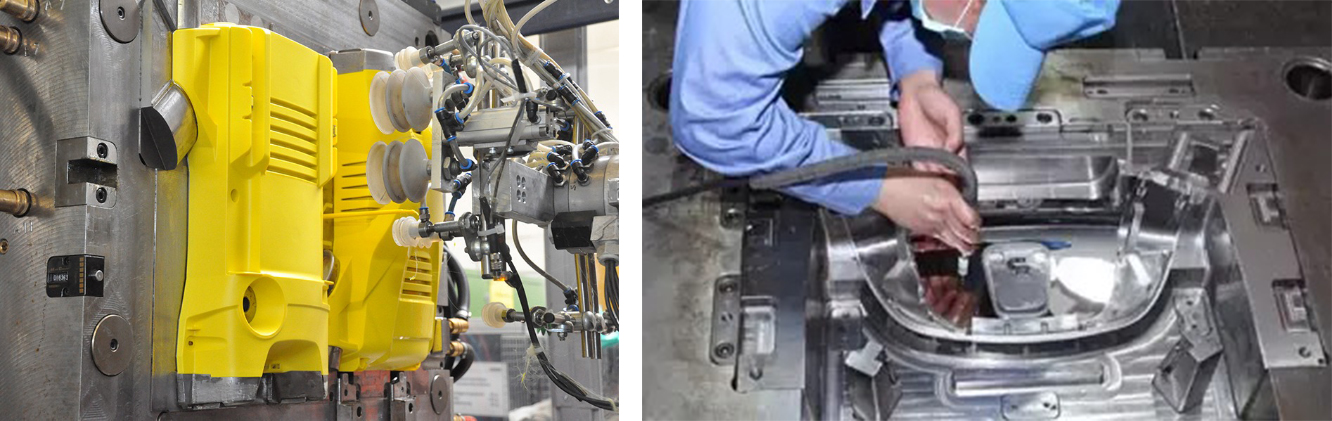
Maintain Stable Mold Temperature
Set an appropriate mold temperature according to different plastic materials and product requirements. During the production process, closely monitor the changes in the mold temperature to ensure that the temperature remains stable within the set range.
Regularly check the heating and cooling systems of the mold to ensure their normal operation. If problems such as damaged heating pipes or blocked cooling water channels are found, they should be repaired in a timely manner.
Control the Injection Pressure and Speed
Reasonably adjust the pressure and speed of the injection molding machine to avoid the impact and wear on the mold caused by excessive pressure and too fast speed.
Monitor the pressure curve and speed curve during the injection molding process to ensure their smooth change and avoid sudden changes.
Regularly Clean the Mold Parting Surface
During the production process, the mold parting surface is prone to accumulate plastic residues and dust, which will affect the mold closing accuracy. Therefore, the parting surface should be cleaned regularly to keep it clean.
When cleaning the parting surface, a copper brush or soft cloth can be used to gently wipe it, and avoid using hard tools to scratch the parting surface.
Thoroughly Clean the Mold
After the production is completed, the mold should be removed from the injection molding machine and comprehensively cleaned. Use mold cleaning agents and tools to thoroughly clean the plastic residues, oil stains, etc. inside the mold.
For parts that are difficult to clean, methods such as ultrasonic cleaning or chemical cleaning can be adopted. However, pay attention to selecting suitable cleaning agents to avoid corroding the mold.
Check the Wear Condition of the Mold
Carefully check all parts of the mold, especially the parts prone to wear, such as the core, cavity, slider, inclined lifter, etc. Observe whether there are situations such as wear, cracks, and deformation.
For slightly worn parts, polishing and repair can be carried out; for severely worn or damaged parts, parts should be replaced in a timely manner or major mold repairs should be carried out.
Apply Rust Preventive Agent
The cleaned mold should be applied with a rust preventive agent in a timely manner to prevent the mold from rusting. Select a suitable rust preventive agent and evenly apply it on the mold surface and moving parts.
After applying the rust preventive agent, the mold should be stored in a dry and ventilated place to avoid a humid and high-temperature environment.
In conclusion, the maintenance of injection molds requires comprehensive management and maintenance in three stages: before production, during production, and after production. Only by doing a good job in mold maintenance can the normal use of the mold be ensured, its service life be extended, and production efficiency and product quality be improved.
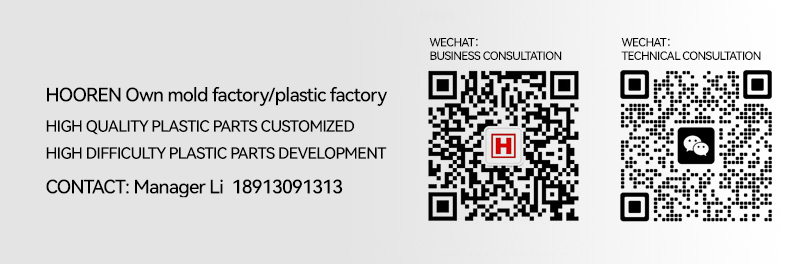