注塑產(chǎn)品熔合線的原因是什么
2025-02-13 16:33:20
注塑熔合線問題
注塑產(chǎn)品出現(xiàn)熔合線的原因是多方面的,主要與塑料材料特性、模具設(shè)計、注塑工藝參數(shù)以及產(chǎn)品結(jié)構(gòu)等因素有關(guān),以下是具體介紹:
流動性:不同種類的塑料具有不同的流動性。像聚乙烯、聚丙烯等結(jié)晶型塑料,在熔融狀態(tài)下流動性較好,而聚碳酸酯、聚苯醚等非結(jié)晶型塑料流動性相對較差。流動性差的塑料在充模過程中,熔體前鋒推進(jìn)速度不一致,容易在匯合處形成明顯的熔合線。
熱穩(wěn)定性:熱穩(wěn)定性不佳的塑料在高溫注塑過程中容易發(fā)生降解、交聯(lián)等化學(xué)反應(yīng),使熔體的性能發(fā)生變化,影響其流動和融合性能。例如,聚甲醛在高溫下容易分解,產(chǎn)生的小分子氣體等會干擾熔體的正常流動,促使熔合線的形成。
添加劑的影響:為了改善塑料的性能,通常會添加一些添加劑,如填充劑、增塑劑、阻燃劑等。填充劑的加入可能會降低塑料的流動性,使熔體在流動過程中更容易出現(xiàn)停滯和匯合現(xiàn)象,導(dǎo)致熔合線明顯。例如,在聚丙烯中加入碳酸鈣填充劑后,熔體的流動性下降,熔合線問題可能會更突出。

澆口位置與數(shù)量:澆口位置和數(shù)量直接影響熔體的流動路徑和匯合情況。如果澆口位置不合理,使得熔體在模具型腔中流動距離過長或流動方向復(fù)雜,就容易出現(xiàn)熔合線。例如,當(dāng)采用單點澆口時,熔體從澆口向四周輻射流動,在相對的兩側(cè)熔體匯合處容易形成熔合線。而多澆口設(shè)計如果澆口分布不均勻或澆口大小不一致,也會導(dǎo)致熔體流動不平衡,產(chǎn)生熔合線。
流道設(shè)計:流道的形狀、尺寸和粗糙度等對熔體流動有重要影響。流道過窄或過長,會增加熔體的流動阻力,使熔體流速降低,不同部位的熔體到達(dá)匯合點的時間差異增大,從而加劇熔合線的形成。
排氣系統(tǒng):模具的排氣不暢是導(dǎo)致熔合線的一個重要因素。在注塑過程中,模具型腔內(nèi)的空氣、塑料揮發(fā)的氣體等需要及時排出。如果排氣不良,這些氣體就會在熔體匯合處形成氣阻,阻礙熔體的正常融合,使熔合線處的結(jié)合力減弱,熔合線更加明顯。

注射速度:注射速度對熔合線的形成有顯著影響。注射速度過慢,熔體在型腔中的流動前沿推進(jìn)速度不一致,先進(jìn)入型腔的熔體溫度降低較快,與后進(jìn)入的熔體之間的溫度差較大,在匯合時就難以充分融合,容易形成明顯的熔合線。
注射壓力:注射壓力不足,無法提供足夠的動力使熔體在型腔內(nèi)快速、均勻地流動,熔體在流動過程中容易出現(xiàn)停滯和匯合現(xiàn)象,導(dǎo)致熔合線。
模具溫度:模具溫度過低,熔體在型腔表面的冷卻速度過快,熔體的流動性迅速下降,在匯合處難以充分融合,形成熔合線。而且模具溫度不均勻,也會使熔體在不同部位的冷卻速度不同,進(jìn)一步加劇熔合線的形成。
保壓時間與壓力:保壓時間過短或保壓壓力不足,在冷卻收縮過程中,熔合線處的熔體得不到足夠的補充,會出現(xiàn)收縮凹陷,使熔合線更加明顯。
壁厚變化:產(chǎn)品壁厚不均勻是導(dǎo)致熔合線的常見原因之一。在壁厚較厚的區(qū)域,熔體流動速度相對較慢,而在壁厚較薄的區(qū)域,熔體流動速度較快。當(dāng)不同壁厚處的熔體匯合時,就容易形成熔合線。
形狀復(fù)雜性:產(chǎn)品形狀越復(fù)雜,熔體在型腔內(nèi)的流動路徑就越復(fù)雜,熔體需要經(jīng)過多個轉(zhuǎn)折、分支等才能充滿整個型腔。在這些過程中,熔體容易在不同流動路徑的匯合處形成熔合線。
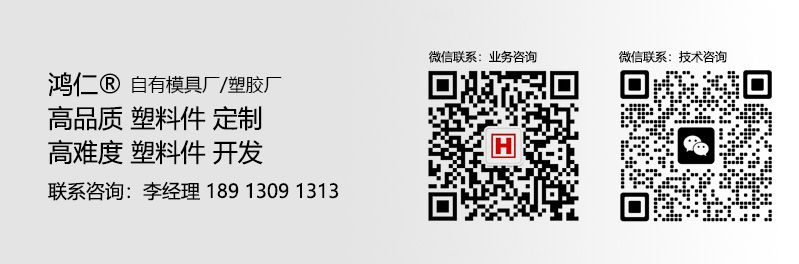